Cooling tower safety vs optimization: The operational and safety aspects of cooling towers
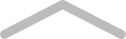
Cooling tower safety vs optimization: The operational and safety aspects of cooling towers
Cooling towers are water-to-air heat exchanging material used to discharge the waste heat from processing industries in to the atmosphere. They have different sizes ranging from small roof-top units to extensive hyperboloid structures that may be as large as 200m and 100m diameters, or can be rectangular constructions that may be more than 40m tall as well as 80m in length.
If operating well, they aid in plant safety while their breakdowns can result in to severe accidents because of overheating. Their cost of functioning is the total of the water and air transportation costs, and hence if these costs are minimized, the plant operating cost can be lowered to a fair amount.
Cooling tower terminology and functioning
Here, you are going to discover the levels of safety and reliability that various cooling tower designs can provide as well as the control systems that can lower their cost of functioning through optimization.
All cooling towers make the best use of the chimney effect, which transports the outside air through the tower. The air moved triggered by the chimney effect bases on the difference in density between the incoming colder outside air at the bottom as well as the air inside, that is less dense since it is warmer and more humid.
The air humidity increases as the air goes up in the column because water continues evaporating provided its temperature its temperature is above the wet-bulb air temperature of the air. This evaporation reduces the density of the inside air and also brings some losses in the circulated water, that requires makeup.
As the water heat is transferred to the air, the lower density inner air goes up and draws in the fresh air at the tower base. In natural draft towers, the air flow is brought about by only the chimney effect. For mechanical draft towers, the air flow is steered by fans, that are at the top of the tower and pulling the air, or are at the bottom forcing the air through the column.
The hotness and coldness of the water supplied to the factory by the cooling towers is typically higher as compared to the wet-bulb temperature of the air that cools it down. In case your thermometer bulb is sheltered by a wet-water sucking up substance and is revealed to air, evaporation will chill the bulb to one of the two thermometers of a psychrometer.
In case the air is soaked with water, the dry bulb as well as the temperatures varying basing on pressure and humidity will all be similar. https://www.saracoolingtower.com/ can provide more information regarding this.
The cooling tower system safety
The safety of all cooling systems rises as the number of their components lowers. The proper functioning of conventional industrial cooling tower structures relies on the availability and proper functioning of the air transportation fans along with the water transportation pumps.
To maximize safety, the most crucial factor is the availability of the power supply to these components. Using natural means, safety can be improved by backup power sources like diesel, turbines, and batteries among others although these backups can sometimes fail to deliver.
A cooling system made up of several components is most likely not safe. Because of this phenomenon, the unsafe cooling system is one that utilizes chilled water. Here, the process heat is initially transferred to the chilled water and then moved from the chilled water to the cooling tower water and lastly it is transferred in to the air. It is not very safe since it is made of four components including; cooling tower pumps, chilled water pumps, chillers, and cooling tower water pumps, each of which can possibly fail or lose its power supply.
The safety of a manufacturing unit will be increased once the process can be redesigned to function directly with cooling tower water to let the chiller get eliminated. Alternatively, once the cold water generated by the tower is not cold enough, it must be sent to the chiller for more cooling before it can be sent to cool the process.
Direct usage of cooling tower water contributes to the safety of the factory as its functioning only needs the proper functioning of cooler tower fans and fans. Such cooling towers are mostly used in large scale industries.
Conclusion
Cooling tower safety is essential for the proper functioning of machines that do vigorous processing tasks.
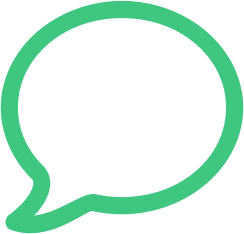