10 Steps Involved In Investment Casting
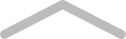
10 Steps Involved In Investment Casting
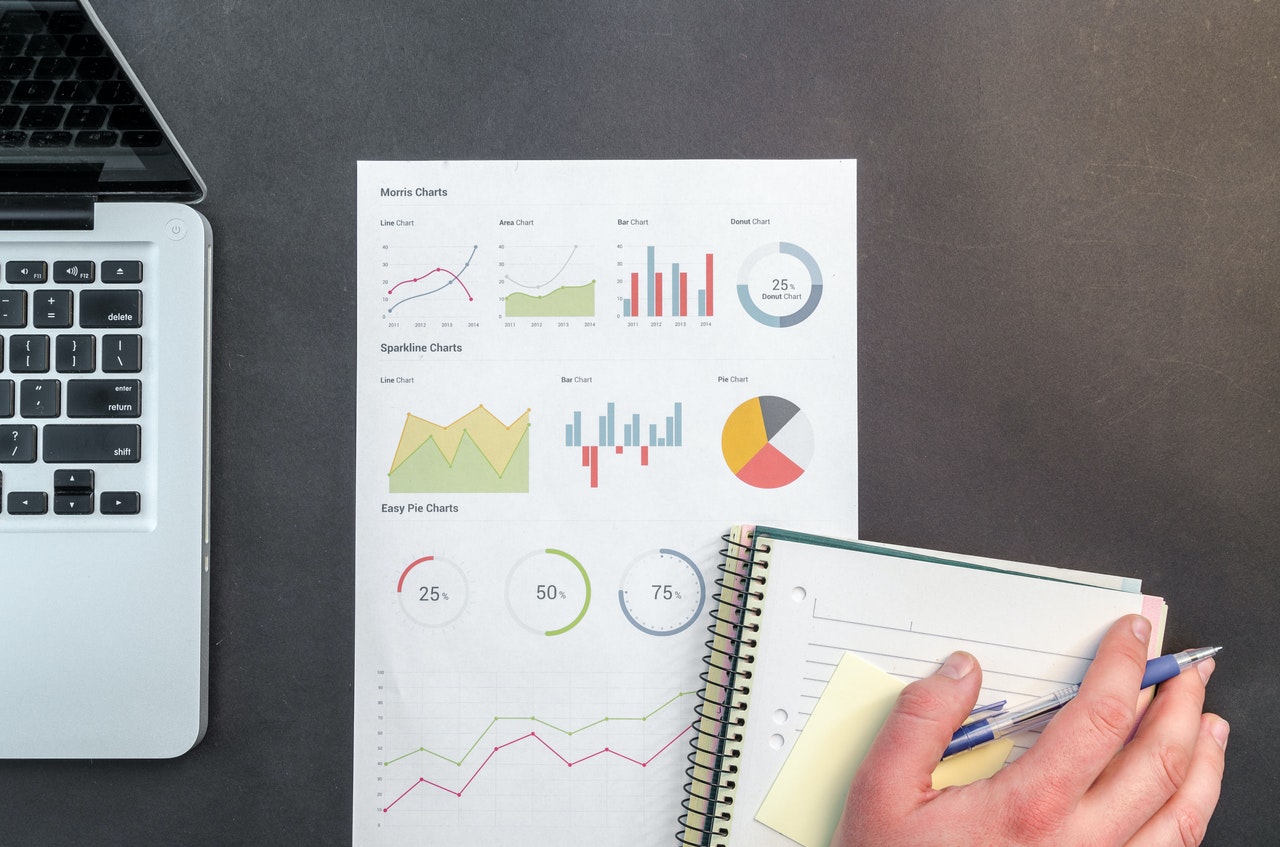
Investment casting is the most common method of metal production. In this method, casting can either be made from the original wax or from other replicas of wax of the original pattern. The process through which casting is made from the original wax is known as the direct method whereas the process where casting is made from the wax replica is known as the indirect method. It can take up to one week to fully complete the process of investment waxing. The process of casting through the indirect process follows the steps below.
Production of the Original Pattern
The first step of casting involves the production of the original pattern. This is where the artist creates an original pattern by molding though wood, clay, and wax or even by using plastic. In other cases, artists also use any material of their choice as long as they have an original plan of how they want the final product to be. However, the production of the original patterns in investment casting has been made much easier in the recent years. Unlike the past when patterns were physically drawn, in the recent years patterns are produced through a 3-Dimension printing. This type of production has become very popular because it is known to produce high resolution patterns.
Creation of the Mould
After the original pattern has been produced, the next step is to create the mould. The mould is usually made in such a way that it fits perfectly in the original pattern. For instance, if the original pattern was made from steel, then the mould, also known as the master die, can be cast directly from the same pattern but using a metal that has a lower melting point. Alternatively, other artists also prefer to create a mould independently without having to create the original pattern first.
Production of the Wax Patterns
This is the third step that is involved in the process of investment casting. Wax pattern is a term that is used to refer to pattern materials including plastic and even frozen mercury. There are two methods of producing wax patterns. The first method is where the wax is poured into the mould and swished around until an even coating is achieved. This method is repeated until the desired pattern is achieved. The second method is where the entire mould is filed with the molten wax and allowing it to cool until it forms a solid method. The method that an artist chooses to sue depends entirely on his needs and expectation of the final product.
Bringing together the Wax Patterns
This is the fourth step in investment casting where the already created multiple wax patterns are assembled to form one large pattern to be cast in one pour. To effectively attach the patterns, a heating tool is used to slightly melt the wax surface that are lying against each other. The end result is then left to cool so that it can harden.
Application of the investment materials
The production of the ceramic mould, also known as the investment is done through the process of repeating a series of steps which involves coating, stuccoing and hardening. This process is done until the desired thickness is achieved. In the first step, fine materials are used to help in the preservation of the fine details from the mould. In the second step, coarse ceramic materials are applied by dipping the patterns into a fluidized bed, and the last step allows the coatings to cure.
Dewaxing
This is the process that involves turning the ceramic moulds upside down by placing it in a furnace only after they have been fully cured. The aim is usually to melt out and vaporize the wax. This is the stage that most of the failures in production occurs. This is because when the wax is heated, it expands and introduces stress. The wax is heated as rapidly as possible so that these stresses can be minimized. This in turn creates more space for the rest of the wax to expand.
Burnout Preheating
After the process of dewaxing, the mould is then subjected to the process of burnout where it is heated to remove any moisture and residual wax. In some instances, the mould is heated before pouring and in other instances, it is allowed to cool so that it can be tested. The benefit of preheating is that it allows the metal to stay in liquid state for longer so that it can perfectly fit the mould pattern and to increase accuracy.
Pouring
After the mould has been preheated, and it is now in liquid form, the mold is placed with the open side up into a tub that is filled with sand. The metal can then be poured by the use of gravity and forced into the mold by applying positive air pressure or other forces. Some of the examples of the methods that use additional force include tilt casting, vacuum casting and pressure assisted pouring.
Divesting
This is the process where the shell is hammered, blasted, waterjeted or chemically dissolved in liquid nitrogen to release the casting. After this has been done, the sprue is then cut out and recycled, and then the process of grinding is incorporated. This is usually done to clean up the casting and to remove any signs of the casting process.
Finishing
This is the final step of the investment casting. After grinding, the now complete casting is subjected to finishing. In the finishing process, the impurities and negatives in the casting are removed through welding and hand tooling. If at this stage it is realized that the casting needs additional straightening, then the process is done by hydraulic straightening press. This procedure brings the final product in line with the tolerances.
In summary, the above is the process that is involved in investment casting. When followed step-by-step, the finished product is usually the way it was envisioned in the creating stage. Therefore, investment casting is the best form casting to use for smooth finished products with different shapes.
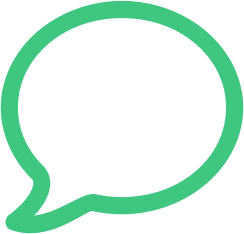